From digital design to finished mold – seamless, end-to-end workflow in the Die & Mold industry
Die & Mold making is a key industry and forms the backbone of modern manufacturing. It develops and produces high-precision tools and molds that are essential in sectors such as the automotive, medical technology, aerospace and consumer goods industries. However, manufacturing companies in the sector are facing increasingly intense global competition and enormous cost pressures that threaten to squeeze companies' margins. At the same time, however, the quality requirements for production are constantly increasing: customers expect maximum precision, perfect surfaces and a long service life for dies and molds.
Initial Situation
The industry is therefore faced with the need to ensure maximum precision, quality and efficiency in its manufacturing processes in order to meet the constantly growing demands. DMG MORI helps companies to meet the high demands placed on production and supports them throughout the entire process as a reliable and experienced partner.
Companies in the Die & Mold making industry are characterized by rapid and dynamic market developments. They are faced with the challenge of asserting themselves in a globalized competitive environment characterized by cost pressure and ever shorter development cycles. In addition, the industry is struggling with the current challenges facing the automotive industry, with the result that many companies have overcapacity in their production. High wage, energy and hardware costs as well as a dwindling supply of available skilled workers are placing an additional burden on many companies, which is why capacities are increasingly being relocated to cheaper production countries.
In addition to these challenges, Die & Mold making is significantly influenced by a number of developments in manufacturing: production processes and components are becoming increasingly standardized in order to increase efficiency and minimize errors. The issue of sustainability is also becoming increasingly important. Companies are progressively required to produce more resource-efficiently, optimize their energy efficiency and reduce the carbon footprint of their products. Additive manufacturing (3D printing) is also being used more and more in Die & Mold making, as it enables the production of complex geometries and significantly shortens process chains. At the same time, the importance of multi-axis machining is also increasing in the industry, particularly 5-axis milling: it offers new possibilities for manufacturing by enabling the machining of complex free-form surfaces in a single clamping operation. These trends require companies not only to invest in modern technologies, but also to continuously train their specialists.
For these trends and challenges, companies need partners who know their industry and can support them with these challenges. DMG MORI has been active in Die & Mold making for many years and knows the industry like no other.
Die & Mold – Quality is a must
Production in Die & Mold making places the utmost demands on the quality and performance of the end products. The highest surface qualities and accuracies are paramount here. Even the smallest deviation in the shape or surface quality of a tool can have a significant impact on the quality of the series parts that are subsequently produced with it. This requires the use of state-of-the-art machining technologies and precise measurement technology. Precision is the fundamental prerequisite for maintaining tolerances in the micrometer range.
Flexible and powerful solutions are in demand
In addition, the complexity of production components is constantly rising and flexible, high-performance solutions are increasingly in demand. The use of difficult-to-machine materials, such as high-strength steels or innovative alloys, requires special machining strategies and extremely stable machines. Finally, meeting exceedingly short delivery times is also a constant pressure factor, as tools are often critical components in customers' development processes. These requirements make a consistent, reliable and at the same time highly flexible production chain from design to finishing essential.
Value Added
DMG MORI – the ideal partner in Die & Mold making
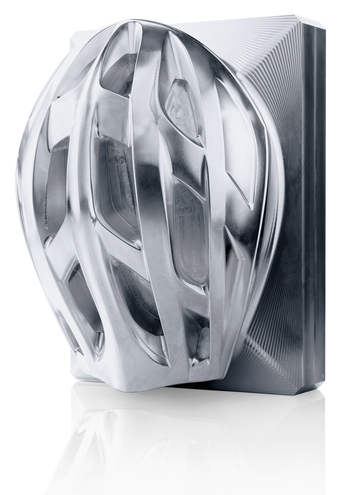
In view of these diverse and demanding challenges, DMG MORI offers manufacturing companies in the industry decisive added value that goes far beyond the mere supply of machines. Our approach is based on a profound process integration that optimally interlinks all steps from planning and design to the finished tool surface. Our LASERTEC 65 DED hybrid, for example, combines additive and ablative technologies in one and the same machine. This combination allows worn material to be removed during the repair of mold cores and then rebuilt in the same machine. Solutions like these enable our customers to optimize their value chain and minimize sources of error at the same time.
A key aspect of this is the consistent automation of production processes, for example through the use of AMR solutions, pallet changers or autonomous production cells. This not only leads to a significant increase in productivity and efficiency, but also to a reduction in the workload of skilled workers and the possibility of unmanned operation around the clock. DMG MORI also has the right solutions in its portfolio for interlinking machines, such as the LPP system.
We also support our customers on the path to Digital Transformation (DX). With our intelligent software solutions and networking options, we enable transparent and data-based production, for example with the help of MPC 2.5 - Machine Protection Control. This ranges from the simulation and optimization of machining processes to predictive maintenance, which minimizes downtimes and maximizes operational reliability.
Last but not least, as part of the Green Transformation (GX), we develop and offer energy-efficient machines and technologies that reduce the consumption of resources and thus support our customers' sustainability goals. From minimizing energy consumption during operation to innovative flow monitoring systems, our solutions help to reduce the ecological footprint of Die & Mold production while strengthening competitiveness.
Your advantages as a customer of DMG MORI
To meet the specific requirements of the Die & Mold sector, DMG MORI offers a comprehensive portfolio of machines and integrated solutions that guarantee maximum precision, productivity and surface quality.
- 5-axis universal machining centers such as the DMU monoBLOCK and DMU duoBLOCK series are essential for machining complex free-form surfaces in a single clamping operation. They impress with their stability, dynamics and simultaneous 5-axis capability. The HSC (High Speed Cutting) machines and eVO series with spindle speeds of up to 60,000 min-1 are used for applications that require maximum cutting performance and excellent surface finishes. They are ideal for the fast and precise production of hard materials.
- The DMU gantry series offers solutions for processing large parts weighing up to 150 tons. These are often required in mold making for the automotive or aviation industry.
- The range is complemented by innovative technologies such as the LASERTEC Shape machines for high-precision laser ablation of surfaces. They offer an environmentally friendly alternative to traditional etching processes.
- The range is complemented by innovative laser technologies, with the LASERTEC 50 Shape with femtosecond laser offering high-precision laser ablation of surfaces on advanced materials. The LASERTEC DED hybrid series is the perfect solution for repair applications in Die & Mold making. Worn tool molds can thus be repaired.
In addition to automation solutions such as pallet changing systems and robot-assisted cells, we also offer software solutions such as CELOS and special technology cycles for optimum machine control and process monitoring. This interplay of machines and solutions enables our customers to make their manufacturing processes in toolmaking future-proof and competitive.
DMG MORI customers also receive a wide range of services: Our comprehensive service and support services as well as our presence in over 40 countries worldwide ensures that companies can always make optimum use of their machines.